Aluminum Homogenising Furnace
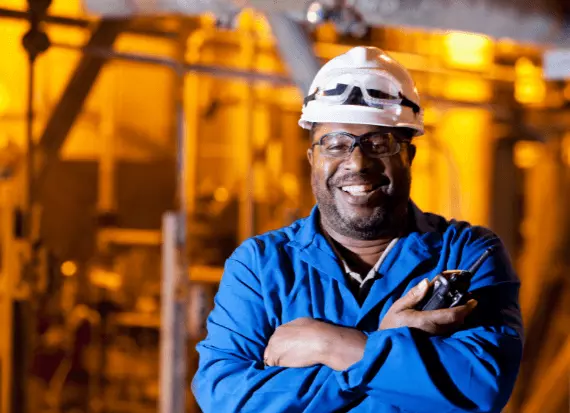
Aluminum Homogenising Furnace
ACME Furnace specializes in custom-engineered aluminum log and billet homogenizing furnaces designed to meet the specific requirements of various process applications. Our batch-type furnaces typically employ an electrically driven insulated bogie for loading and unloading materials. To enhance efficiency and minimize turnaround time, we often utilize double-ended furnaces with two bogies, allowing for simultaneous loading and unloading.
As an alternative to the car bottom design, our batch-type furnaces can also be configured with a tray design. In this configuration, the load tray rests on a series of support piers within the furnace. A dedicated charge machine or transfer car is employed for loading, unloading, and transferring trays between the furnace and cooling or loading/unloading stations.
For certain applications, we offer traveling furnace designs, which provide flexibility and efficiency for various process requirements.
ACME Furnace offers innovative traveling furnace designs that optimize efficiency and productivity. Our furnaces utilize a pair of fixed load bases to support the load, enabling continuous operation without downtime. As one load completes its cycle, the furnace moves to position over the second load base, immediately beginning the heating process for the new load. This allows for efficient cooling and reloading of the previous load, maximizing throughput.
Our patented reversing airflow design incorporates upstream/downstream temperature control using an axial flow fan wheel that reverses rotation on a timed basis. This alternating airflow pattern ensures uniform heat distribution and improved temperature control throughout the load. A thermal head is employed during the initial stages of the cycle to accelerate heating, resulting in faster heat-up rates and improved temperature uniformity. This design enhances efficiency, reduces fuel costs, and optimizes metallurgical results.
To further enhance performance, our furnaces feature adjustable airflow baffles, a patented innovation by ACME Furnace. These movable baffles effectively limit or block open spaces above the load, optimizing airflow distribution and preventing short circuiting. This results in faster heat-up rates, reduced energy consumption, and improved temperature uniformity throughout the load.
We understand the importance of efficient cooling after homogenization, and our furnaces offer a variety of cooling options to meet your specific requirements. Our load cooler designs include one-way airflow, reversing airflow, air/mist arrangements, and other configurations to ensure uniform cooling and prevent warping or bowing of the logs or billets. The cooling rate can be precisely controlled using variable speed cooling fans.
- Temperature Range – Upto 1100°C
- From 50 to 1500 KW
- Batch capacity upto 200 MT.
- Insulation – Vacuum Formed Ceramic Fibre Boards / Ceramic Fibre Blanket & Module / Brick Lining
- Heating Media Options – Electric / Gas Fired / Oil Fired
- Heating Elements – Nichrome Wire /Strip Wire
- Sealing of the vertical lift doors and bogie through pneumatically operated soft seal clamps to ensure no ingress of cold air.
- Furnace Classification – Class 2 / Class 3
- Instrumentation – Thyristor, Programmable Temperature Controller, Temperature Recorder, PLC, SCADA, HMI
Homogenizing of Aluminium and Billets