Roller Hearth Furnace
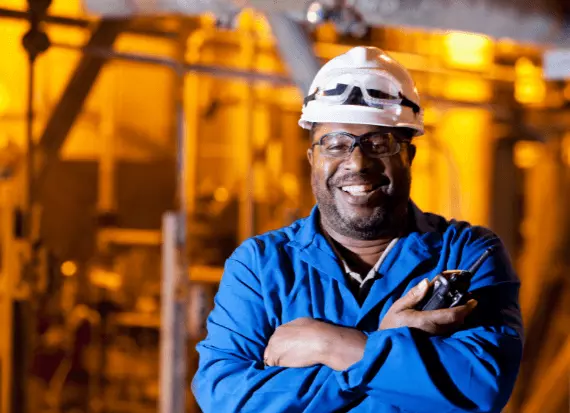
Roller Hearth Furnace
ACME Furnace designs roller hearth furnaces to economically heat treat a wide variety of products with uniform and repeatable results. Available in a wide range of sizes, these furnaces come with either electric or fuel-fired heating systems, along with matched cooling sections and material handling systems. When paired with a protective atmosphere to maintain product cleanliness or enhance surface treatments, ACME Furnace’s roller hearth furnaces offer a highly efficient solution for today’s manufacturing needs.
Continuous, Unlimited Workflow:
The roller hearth conveyor system operates through a series of externally driven rolls, eliminating the cumulative pressures and tensions found in belt, chain, or pusher furnaces. As a result, there are no limits on production or cycle time, and the furnace length can be customized to meet your specific application needs. Each roll section operates independently, enabling continuous or interrupted workflows.
Fast, Top-Quality Production:
The advanced design of these roller hearth furnaces enhances both production speed and quality. Individually driven roll sections ensure quick material flow, while heavy-duty insulation systems, welded gas-tight casings, and temperature-engineered doors guarantee fast, precise, and uniform heating and cooling. This design minimizes heat loss, atmosphere mixing, and product distortion or stress.
Ease of Installation:
Furnace sections come fully assembled from the factory, complete with insulation, heating systems, piping, wiring, and rolls. Skid-mounted sections are easily moved, welded or bolted together, and quickly put into operation. Factory assembly by skilled staff ensures superior craftsmanship, reducing potential issues often encountered with on-site construction.
Extended Component Life:
Because the individual conveyor rolls are externally driven and remain within the same temperature zones, they avoid thermal cycling and are built for maximum durability at operational temperatures. The absence of cumulative pressures on conveyor rolls, work trays, and workloads further extends the life of the components. Specially constructed furnace doors are insulated to withstand the temperature zones where they are located, minimizing stress and warping. High-quality components in the heating and cooling sections ensure long-lasting, dependable operation.
Flexible Operation:
Each roll section can be independently started, stopped, reversed, or oscillated, allowing for flexible production. Sections can run at uniform or varying speeds, ensuring efficient use of furnace space. High-speed transfers between sections enable closely spaced workloads or trays to be separated during transitions through doors, optimizing hearth space and minimizing atmosphere mixing. Adjustable door openings accommodate different workload heights, speeding up operations while preserving atmospheric integrity.
Lower Product Costs:
A wide variety of furnace combinations and sizes ensures you can find a furnace tailored to your specific needs. Increased product quality and production rates reduce costs, and factory assembly lowers installation expenses, allowing your furnace to start production more quickly. The use of premium materials and expert design minimizes maintenance, further driving down operational costs.
Cycle Annealing:
Cycle annealing creates a strong, uniform steel structure and is typically used to enhance the machinability of screw machine stock, improve cold working properties in deep drawing stock, and boost impact resistance and fatigue strength in gears or machine parts. The furnace heats steel to just above the hardening temperature (around 925°C), cools it rapidly to the transformation temperature (approximately 650°C), holds it until the transformation occurs, and then cools it down. Roller hearth furnaces can be gas-fired or electrically heated and are often equipped with a controlled atmosphere to prevent scaling and surface decarburization. Maximum furnace temperature: 950°C.
Annealing, Hardening, Preheat, Normalizing, Stress relieving, Bright Annealing Furnace