Ageing Cum Annealing Furnace for Aluminum
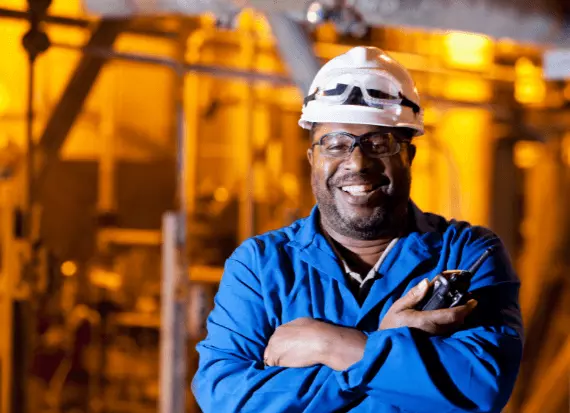
Ageing Cum Annealing Furnace for Aluminum
ACME Furnace is a leading provider of high-quality batch-type bogie hearth furnaces, designed to meet the specific needs of annealing aluminum alloy conductors and aging AAAC conductors and aluminum alloy wire loaded on drums. Our furnaces are available in a wide range of capacities, up to 50 MT, ensuring optimal performance for various applications.
To facilitate efficient heat distribution and energy conservation, we employ advanced recirculation systems. Our furnaces are equipped with either axial or centrifugal recirculation fans, which can be configured with two-speed motors or variable frequency drives (VFDs) for precise control and reduced energy consumption. Stainless steel baffles are strategically placed within the furnace chamber to ensure uniform air circulation and prevent cold spots.
For accelerated cooling, our furnaces can be equipped with forced air-cooling systems that utilize centrifugal fans to rapidly dissipate heat and reduce cooling times. This feature is particularly valuable for applications that require quick turnaround times.
The electrical heating systems in our annealing furnaces are designed for precise temperature control and efficient energy utilization. Strip-type heating elements are strategically positioned along the sidewalls of the furnace, ensuring even heat distribution. The heating elements are divided into multiple zones, each with its own bank of heater cartridges. This modular design allows for individual heater replacement without interrupting furnace operation. The heater banks can be connected in either STAR/DELTA or Parallel STAR/DELTA configurations to optimize energy efficiency and minimize the number of heaters per phase per group.
ACME Furnace specializes in annealing furnaces that incorporate advanced insulation technology to minimize heat loss and maintain optimal operating temperatures. Our furnaces feature a combination of ceramic fiber board and ceramic fiber blankets, backed by stainless steel studs, for the side walls, roof, and doors. This insulation configuration effectively reduces the skin temperature of the furnace, enhancing energy efficiency and operator safety.
For electrically heated furnaces, we employ a sophisticated heat head ratio control philosophy in conjunction with thyristor heater controllers. This approach ensures precise temperature control and optimized energy efficiency. To further enhance energy efficiency, we offer two heating control options: 100% thyristor controllers or a combination of 30% thyristor and 70% STAR-OFF mode, providing flexibility for different heating and soaking requirements.
As an alternative to electric heating, our furnaces can be equipped with high-efficiency burners supported by a comprehensive combustion system, including a combustion fan, atomizing fan, oil heating and pumping systems, and/or gas trains. We incorporate auto ignition, flame failure safety, and complete control systems for reliable and safe operation. Our furnaces can accommodate a wide range of fuels, including Light Diesel Oil, LPG, Natural Gas, or a combination for dual-fired furnaces.
- Temperature Range – Upto 700°C
- From 50 to 1500 KW
- Batch capacity upto 200 MT.
- Insulation – Vacuum Formed Ceramic Fibre Boards / Ceramic Fibre Blanket & Module / Brick Lining
- Heating Media Options – Electric / Gas Fired / Oil Fired
- Heating Elements – Nichrome Wire /Strip Wire
- Sealing of the vertical lift doors and bogie through pneumatically operated soft seal clamps to ensure no ingress of cold air.
- Furnace Classification – Class 2 / Class 3
- Instrumentation – Thyristor, Programmable Temperature Controller, Temperature Recorder, PLC, SCADA, HMI.
Annealing, Ageing which serves for Aluminium alloy conductor manufacturers