Electric Oven
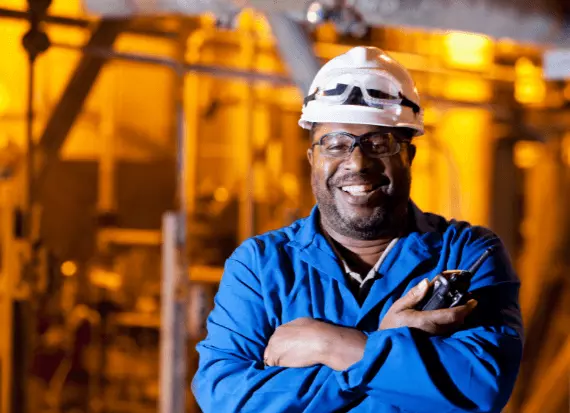
Electric Oven
ACME Furnace has been a prominent manufacturer of electrically heated and fuel-fired bogie, fixed, and continuous ovens for over two decades. We offer a comprehensive range of bogie, fixed, and continuous ovens with capacities of up to 500 MT, catering to industries such as foundry cast houses, heavy engineering, automotive, rail wagons, electrical machines, and other metal sectors. Our ovens operate within a temperature range of 500°C to 4500°C.
The fixed and bogie hearth ovens can be equipped with either single or double door applications, while continuous ovens are designed with double doors to facilitate charging from one end and discharging from the other. Materials are loaded into the bogie hearth ovens using an overhead traveling (EOT) crane or other mechanical devices on the electro-mechanically operated bogie. For fixed hearth ovens, charging can be accomplished using charging machines or air casters, ensuring efficient drying and curing processes.
The continuous ovens can be designed as conveyorized or trolley types. In the conveyorized ovens, the conveyor is operated electro-mechanically, while the trolley-type ovens feature a pusher that can be operated either electro-mechanically or hydraulically. In both designs, materials are loaded at the front end and unloaded at the back after maintaining the required retention time for effective drying or curing.
Electrically heated ovens utilize a heating system featuring resistive cartridge or tubular heating elements positioned along the side, back walls, and roof of the oven. These heating elements are divided into multiple zones based on the oven’s size and are controlled using a PID-based system with thyristor or contactor relay logic.
For fuel-fired ovens, we employ high-efficiency burners supported by a comprehensive combustion system with robust safety arrangements.
Typically, ACME Furnace bogie, fixed, and continuous ovens are lined with mineral wool or ceramic fiber blankets packed between double wall panels on the side walls, roof, doors, and hearth to minimize skin temperature. The inner walls of the ovens can be constructed from mild steel or stainless steel, depending on the required service temperature.
Each oven is equipped with appropriate baffles and recirculation fans to enhance heat transfer through convection and ensure good temperature uniformity. The baffles and fans can be made from mild steel or stainless steel based on the service temperature. Additionally, the drive motors for the recirculation fans are VFD-driven, allowing for soft starting and improved temperature control.
- Maximum temperature 300 ˚C
- Temperature uniformity within +/- 5 ˚C. For aerospace application within +/- 2-3 ˚C.
- Programmable PID controller to achieve close temperature uniformity.
- Type of Ageing Ovens: Double Bogie Heath construction.
- Max. 200˚C for ageing and 400˚C for annealing.
- Temperature uniformity within +/- 5 ˚C.
- Master-slave control with programmable master controller to achieve close temperature uniformity.
Ageing of AAAC conductors and annealing of aluminium alloy wire loaded on drums.