Pusher Type Furnace
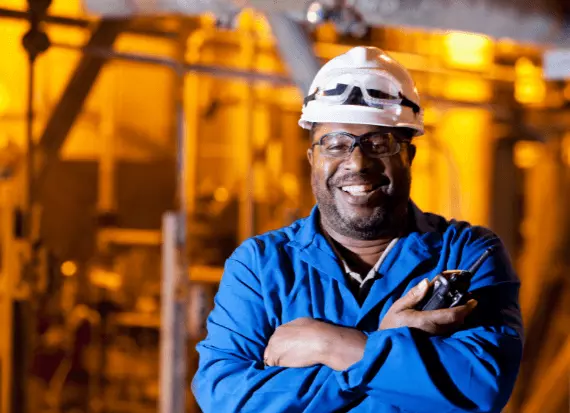
Pusher Type Furnace
ACME Furnace specializes in the production of fully automatic pusher furnaces, engineered to deliver exceptional performance and efficiency. These furnaces are equipped with a range of innovative and unique features that provide maximum flexibility in operation, allowing for seamless adjustments to various heat treatment processes. With high reproducibility, they ensure consistent, precise results across every batch, making them ideal for demanding industrial applications.
Designed with energy efficiency in mind, these pusher furnaces help reduce operational costs by optimizing energy consumption without sacrificing performance. Their robust construction and advanced engineering result in greater uptime, minimizing maintenance and downtime for repairs, which translates into improved productivity for your business.
What sets ACME Furnace apart is the ability to fully customize each pusher furnace to meet your exact heat treatment and processing requirements. Whether you need specific temperature ranges, material handling systems, or additional automation features, these furnaces are tailored to suit your unique needs, ensuring seamless integration into your existing operations while enhancing overall process efficiency.
- Variable Production Rates: Designed to handle varying production rates while processing a large number of different parts.
- Custom Design: Each furnace is tailor-made based on production requirements, component types, process needs, and space availability.
- Heating System Options: Available with either electrically heated or gas-fired systems (LPG, propane, or natural gas).
- Quenching Capabilities: Equipped with free and/or press quenching options.
- Automated Control: Provides fully automatic operation with control, tracking, data monitoring, and acquisition capabilities.
- Furnace Atmosphere Options:
- Endogas with LPG/Propane/Natural Gas.
- Methanol + Nitrogen with LPG/Propane/Natural Gas.
- Compact and Robust Design: Space-saving, fail-safe design with state-of-the-art technology.
- Uniform Temperature Distribution: Recirculation system ensures uniform temperature and atmosphere distribution, enhancing repeatability.
- Flexible Configurations: Available in single or multi-row and single or multi-chamber designs for high flexibility.
- Efficient Insulation: Furnace shell includes lightweight, low heat-retaining insulation and silicon carbide segmented skids to minimize heat loss and maintain low skin temperatures.
- Heavy Load Handling: Pusher mechanisms are designed for handling heavy loads.
- Advanced Control System: Includes temperature and carbon potential control, offering fully automated operation with modern process control interfaces.
- Cost-Effective Quenching System: Option to design with floor-mounted quenching oil and washing machine tanks, avoiding the need for costly civil pits.
- Safety and Ease of Use: High operational safety, easy to operate and maintain.
Pusher furnaces are typically used for thermo-chemical heat treatment processes, making them ideal for handling high-volume production with less variation in product type. These furnaces are well-suited for operations such as carburizing, hardening, annealing, stress relieving, solution treating, and aging. They can process a wide range of parts, particularly in the automotive industry, including transmission and axle components, gears, shafts, castings, drivetrain parts, forgings, and various engine components.
- Our Pusher Furnaces have Ability to handle variable production rates and simultaneously process large number of different parts.
- Compact, Robust, Fail-Safe & Space Saving Design with state-of-the-art technology.
- Recirculation and not agitation leads to uniform distribution of temperature and protective atmosphere leading to best in class repeatability.
- Single and Multi row as well as single and multi chamber design available offering high flexibility.
- Furnace shell equipped with light weight and low heat retaining insulation and provided with silicon carbide segmented skids on hearth minimizing heat loss and low skin temperature.
- All Pusher mechanisms dedicated for heavy loads.
- Advanced temperature and carbon potential Control System leading to Fully automatic control system with interface for modern process control systems
- Can be designed with floor mounted quenching oil and washing machine tanks eliminating costly civil work for pits.
- High operational safety and easy to operate and maintain.